Blog
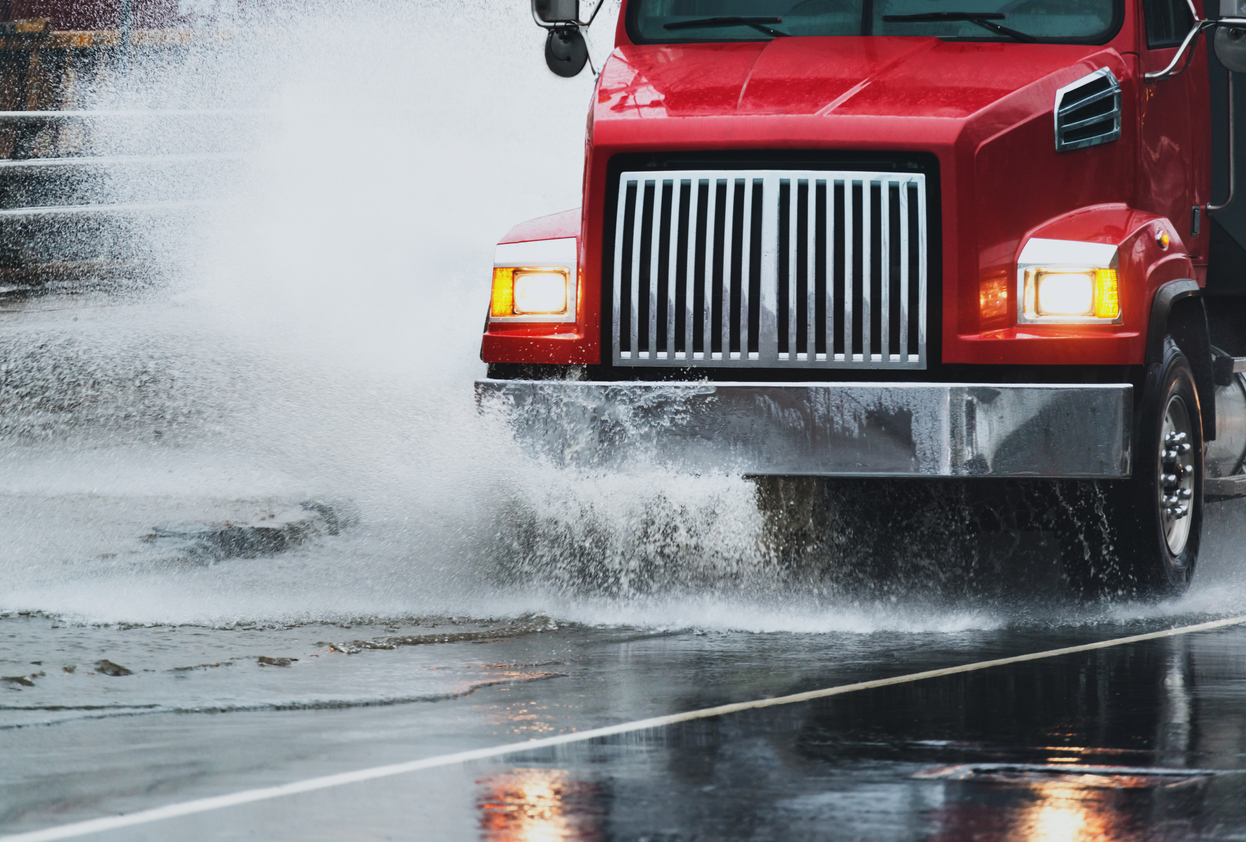
Mar
When the weather starts getting rough, commercial truck drivers have to slow down and take some extra precautions. This can be a little frustrating for other motorists on the road, which may lead to impulsive and dangerous decisions around these trucks.
Poor weather can make driving difficult for a regular passenger vehicle, but commercial trucks have it even harder.
We all have to share the same road, though, so it’s important to understand what sudden weather changes mean for truckers, and what you can do as a motorist to keep everyone safe.
Physics is a Harsh Taskmaster
A commercial vehicle with a full load can easily weigh as much as 80,000 pounds – compared to most passenger vehicles that range somewhere between 3,000 and 4,000 pounds.
Safe to say: trucks are going to handle a little differently.
That much weight can be difficult to control and will cause serious damage in a collision, and when the weather turns bad, it only makes handling even more of a challenge.
In normal weather, a 4,000-pound vehicle travelling at 65 mph can take up to 316 feet to stop. That’s a bit longer that the length of a football field. A fully loaded commercial truck, on the other hand, going at the same speed will take nearly twice that length (around 525 feet) to stop.
But it’s more than just weight that affects how well a truck can stop in winter.
Brake lag is also something drivers need to consider. Brakes on a large commercial truck don’t work like those ones in passenger vehicles. When you step on the brakes in the car, the hydraulic systems react instantly. The air brakes in semi-trucks, take a little more time to apply pressure.
This lag time can make it harder for a truck driver to stop in time to avoid a collision with a vehicle that doesn’t give it enough space.
“What Is That Truck Doing?”
This is a phrase that a lot of motorists think when they’re driving behind a large truck – especially when it appears to them that the weather “isn’t that bad.” Afterall, it’s “just a little rain or snow.”
But a little rain and a little snow means a lot more to a truck driver (see above to understand why), which is why they make some specific choices about how they’re driving.
Motorists need to be aware of what they’re thinking to make the best possible choices for their own safety.
Truck drivers must reduce their speed when they’re driving through poor weather conditions. And, if the situation continues to get worse, they are required to pull off the road and wait until the weather clears.
Passenger vehicles need to keep an eye out for them on the side of the road and be aware that they may choose to pull off the road.
Truck drivers are also going to brake and accelerate lightly to avoid locking up their tires and going into a spin, which also contributes to the time it takes to start and stop. Drivers will also try to create extra space on the road between them and other vehicles, so they may decelerate at unexpected times.
Tips for Passenger Vehicles around Commercial Trucks
These tips come straight from the Federal Motor Carrier Safety Administration. They provide some simple guidelines for staying safe around commercial motor vehicles. Be sure to check out the site for full details (and great graphics that help illustrate these points), but the highlights include:
- Stay out of the blind spots. Commercial trucks have huge blind spots that extend across multiple lanes and back dozens of feet. Basically, if you can’t see the driver in the vehicle’s side mirror, you can safely assume that the driver can’t see you, either.
- Pass carefully. Signal before you start to move and then accelerate so you can get past the truck safely and quickly. Don’t linger. Make the choice to move and do it confidently and carefully. If a truck is passing you, give them some space to get back into your lane. Refrain from passing them going down a slope, since they tend to speed up going downhill.
- Don’t cut off a truck. If you’re moving into a lane too quick and too close to the truck, it can be very dangerous. You’re probably already in their blind spot, and if you’re way too close, the truck simply won’t be able to slow down quickly enough to avoid a collision.
- Don’t tailgate. And, if you’re stopped on an incline, be sure to put plenty of space between you and the tractor trailer ahead of you.
- Give them extra turning space. Even when the roads are clear, a truck is going to swing wide when they turn. If there is a slick road under them, it could cause all kinds of other problems. Give them room when they turn, don’t try to get between a turning vehicle and the curb, and never stop in front of the intersection line or “block the box” at an intersection.
- Be patient. Modern trucks have a ton of power and strength, and once they get going, they keep going. However, it’s not going to accelerate as fast as your average passenger vehicle, even on a flat road. It’s important to understand this so you can keep your cool on the road. Getting aggressive and angry about it won’t help anyone and just lead to other risks.
These tips are important in everyday situations. They’re doubly important when the weather turns against you.
Working Together for a Safer Road
Even in bad weather, transportation services have to continue. When the weather changes, it can create a range of new risks, and everyone on the road has the responsibility to drive safely to prevent accidents.
Commercial truck drivers may have more responsibilities than the average motorist, since their trucks weight so much and they to arrive at their destination without damaging their freight. However, drivers in passenger vehicles share the same responsibility to watch out for potential dangers and share the road with everyone.
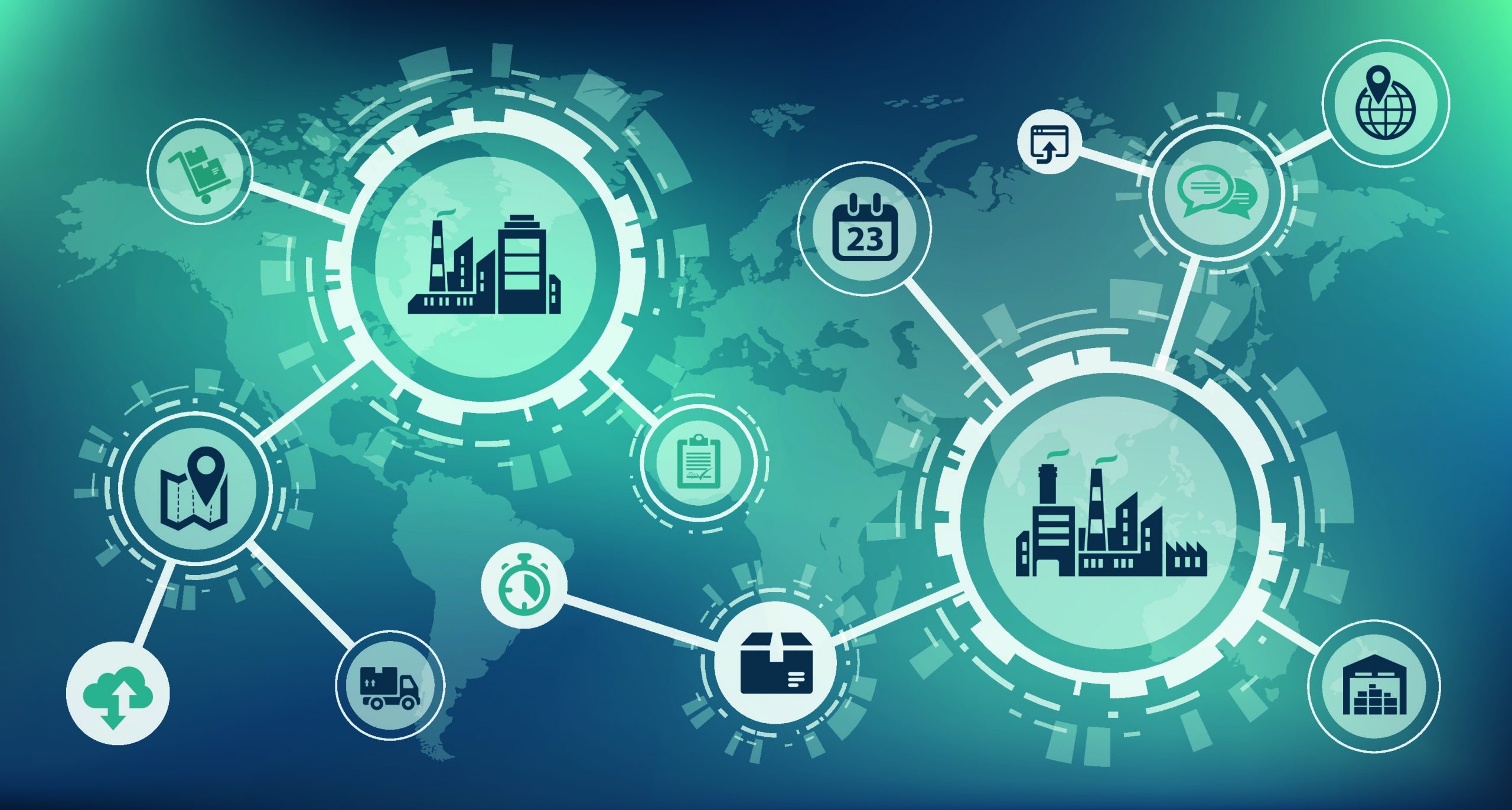
Feb
There are several components of a modern supply chain that can impact a company’s bottom line. You can usually divide these elements into three basic categories: purchasing, manufacturing, and transportation.
Of those three, some estimates suggest that transportation can end up being 60% or more of your total operational costs.
In other words, a shipping company plays a huge role in the effectiveness and profitability of your supply chain. This means that it must always be one of the most prominent parts of your overall supply chain management strategy.
Understanding the Benefits of Effective Shipping Processes
When we say “transportation” we are referring to the entire process of moving your products through the whole supply chain, from the materials that leave a factory, spend some time at a warehouse, and then continue on to the end user.
Since transportation acts as such a critical element of this equation, making it an integral part of your strategy can lead to significant benefits. When everything is working together effectively, you can expect:
- A higher ROI
- Lower overhead
- Better sustainability
- A competitive advantage
- More effective risk management procedures
- Better demand prediction
- Improved efficiencies
- The ability to meet customer demand
It’s also important to note that you should expect your shipping company to consult with you on the most cost-effective options for every shipment and ensure that you are getting the right type of shipping for your products.
Are your products considered perishable? Your shipping company should help you understand everything about refrigerated transportation.
Are there special considerations for seasonal products? Ask about potential challenges for this year’s crop.
The more you treat your shipping company like a real partner, the more you can expect them to help guide you past any potential issues.
Supply Chain Integration
Your ideal shipping company should be able to enhance almost every aspect of your supply chain activities. This is the most effective way to improve your strategy, because you can work with a single company to provide better warehouse management, inbound freight coordination, order fulfillment, and more.
At Calex ISCS, we provide supply chain management solutions that integrate our storage services so that you can do more than just ship your packages. By combining our shipping with our warehousing facilities, you can take advantage of:
- Flexible pricing
- Experienced fulfilment services
- Material handling experts and equipment
- A variety of storage space options
- High-tech security and monitoring
Meeting Customer Demand
Shipping companies have become even more important in the modern, on-demand marketplace. Customers have high expectations for faster deliveries, and that means that your logistics strategies must find a way to live up to those demands.
This could mean looking at shipping companies with warehouses in physical locations that are closer to your customer base. It could also mean using the most recent and sophisticated software systems to track inbound and outbound activities, truck locations, and warehouse space.
Customer satisfaction is going to drive your business growth and your ability to remain profitable. You need to find the best ways to deliver your product on time and without excessive shipping costs.
There are a lot of things that may stand in the way, though. Everything from the ongoing driver shortage to the always-increasing costs of fuel can impact your ability to get your products where they need to go. However, planning for these eventualities from the very beginning can help set you up for success in the long run.
Tracking Your Shipments
In order to ensure that your supply chain is running as smoothly and efficiently as possible, your shipping company should provide reliable and effective tracking solutions.
Logistics companies are responsible for the correct picking, loading, and shipping of your products. This can get even more complicated if there are multiple pick-up and drop-off points along the way.
Any losses due to mistakes in the shipping process can be very costly for the manufacturer and the shipping company, which is what makes a reliable tracking system and important part of every shipment.
Strengthen Your Supply Chain
In order to ensure that your supply chain runs as effectively as possible, it’s critical to partner with a shipping company that understands your business and can deliver on their promises. This means getting your shipping and warehousing services connected with the most up-to-date tracking and automated systems with managers, drivers, and logistics specialists who are committed to fulfilling the demand for your product from start to finish.
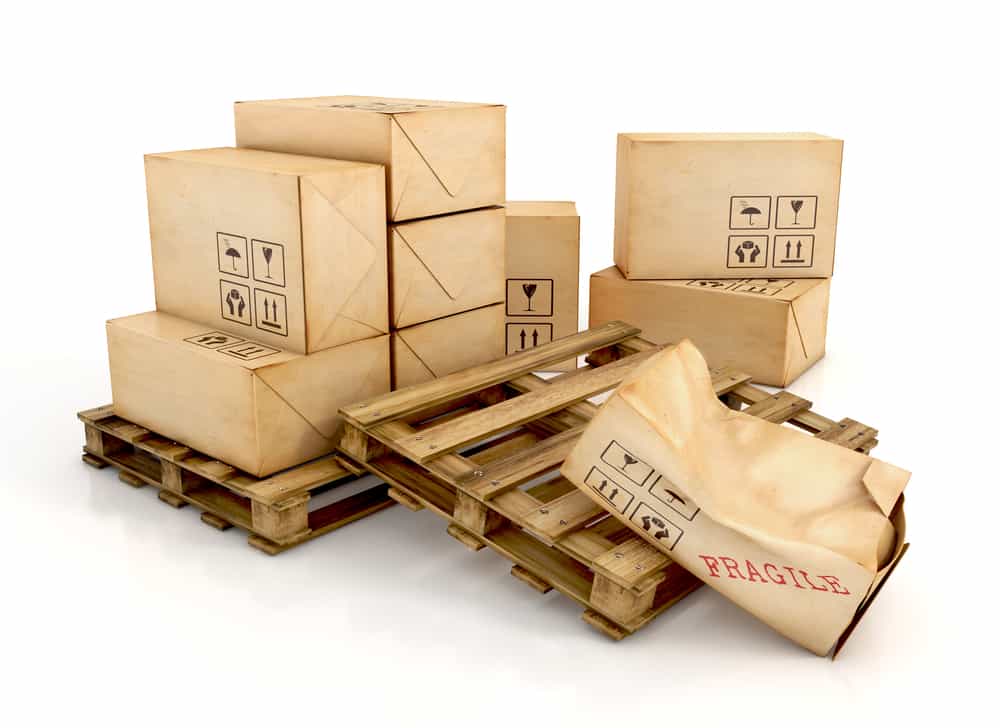
Feb
Lost or damaged freight can cause a huge headache and disruption in your business. Safety is priority one at Calex ISCS because we care about out drivers and their wellbeing. We also care about our clients and ensuring that their products get from point A to point B, on time and in perfect shape using our transportation services.
However, sometimes things happen beyond our control that may cause a shipment to become damaged or lost. Knowing what is covered by carrier liability and what is covered by freight insurance is crucial, as it will directly impact the outcome of the claim you make.
What should you do if your freight becomes lost or damaged?
If you suspect that a shipment has been damaged or lost, the first thing you should do is determine the extent of the damage that occurred. Carefully inspect the freight immediately upon arrival and document any damages you may find. Documentation is critical in making a claim, so the more the better (pictures are recommended, if possible). It’s important to also note the word “damaged” on the bill of lading to ensure the condition is known at the time of accepting the freight. Do not refuse the shipment or discard any damaged product or packaging as this may result in a denied claim or reduced payout.
Finding what’s covered and what’s not.
To understand what is covered and what is not, you must understand the difference between carrier liability and freight insurance. Both are forms of liability coverage, however, with carrier liability, your refund is limited, has several exclusions, and requires the carrier to be found liable for the loss or damage. In order for a carrier to be found liable, you must be able to prove that the damage done was a result of carrier negligence during transportation services. Along with this, the damaged or lost freight must have been properly packaged prior to the carrier picking it up, and there must be a signed delivery receipt on file.
Freight insurance does not require that you prove that the carrier was at fault, just that the damage or loss occurred during transportation services. Additionally, freight insurance oftentimes will cover the entire value of the shipment.
When to make a claim?
Carriers should be notified of any claim as soon as possible. However, if the proof of delivery is noted, you have up to nine months from the date of delivery to file a claim. How long it will take for your claim to be resolved depends on if it falls under carrier liability or freight insurance.
If your claim is covered by freight insurance, it is typically resolved within 45 – 60 days. If your claim falls under carrier liability, it can take more time, as carriers have 30 days to acknowledge the claim, and then an additional 120 days to resolve the claim.
How Calex ISCS can help protect your shipment
Lost or damaged freight can have serious repercussions for some businesses. For this reason, it is important for companies to do everything in their power to reduce the probability of their shipments being lost or damaged when using transportation services.
Through effective logistics management, we can keep your goods flowing smoothly between your company, our warehouses, and the final destination. More importantly, we can do it while keeping our drivers and your products as safe as possible. By putting all of our efforts into improving safety on the road, we are, in fact, improving the efficiency of your supply chain.
By adhering to our road safety protocols, accidents including damaged or lost shipments can be minimized. While we do realize that some accidents simply cannot be avoided, we do everything in our power to do the right thing each and every day. Our knowledgeable team is here to help you navigate the way, should something unforeseen happen to your shipment, resulting in the need to file a claim.
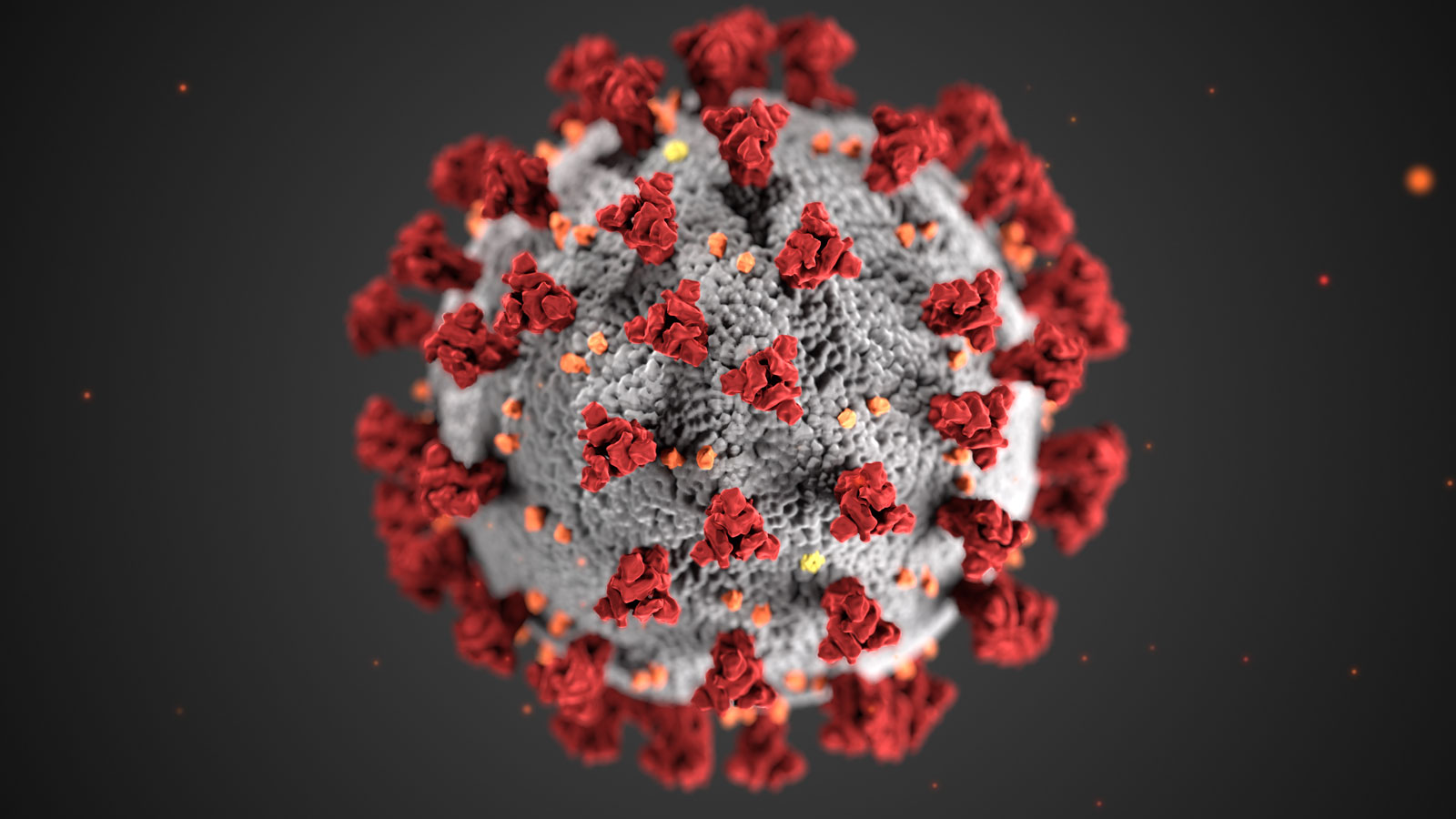
Feb
There’s no doubt that COVID-19 changed just about everything for business owners across the country. Either your own state was subject to strict shutdowns and restrictions or your customers were unable to place an order because they faced the same conditions in their state.
As more and more places open back up, more and more businesses will have to find efficient and effective ways to re-establish their supply chain management processes and get back to freight shipping in a world that still has quite a few added regulations on just about everything.
Every state in which you ship to or from is going to have its own regulations, and it can be a whole new challenge, from a logistics perspective, to navigate all these requirements and try to get back to “business as usual.”
So, what do you need to know about shipping products in the age of COVID?
Here are a few guidelines that we recommend:
Don’t Ignore Regulations
There are still a number of safety requirements on businesses throughout the country. Depending on your location, yours might be a little stricter than others.
However, this is not the time to make a “judgement call” and decide that you are personally exempt from the local regulations.
You don’t want to give the government officials in your area any reason at all to shut back down just when it looks like most things could be opening back up.
So, stick to the plan for now. Go out of your way to prepare your products for shipping while still following all the rules that we’ve had for the last year. Namely: keep using face coverings, follow social distancing guidelines when you can, require proper hand washing hygiene, and keep cleaning and disinfecting areas that are frequently touched.
Your products are going to be shipped to locations all over the country, so it’s likely your business is going to be watched carefully to ensure it’s still following these regulations.
Keep it up for a little while longer and you will soon be back to operating normally.
Evolve Your Shipping Procedures
There’s no better time than the present to re-examine and re-implement your supply chain management strategy.
COVID has changed things for everyone, and you’re going to need to evolve to keep up.
This isn’t always a bad thing. In fact, this may be the perfect time to look at your current strategies, processes, and procedures and find some new places where you can save money or improve efficiencies.
As you start to reopen, consider a few of these tips:
- Some warehouse considerations will contribute to more effective transportation services. Make sure that you are aware of the warehouse security and safety measures.
- Re-evaluate your packaging processes. You can save a lot of money if you are using the correct packages.
- Start shipping from a different location. Plan your shipping routes based on the proximity to the warehouse.
- Plan ahead for seasonal shipping. This is especially important in the produce season. Consumers expect the freshest products, but regulations will be tight on consumables for a long time.
- Ask us a lot of questions. The situation is changing all the time out there, and it can be difficult to keep up with the regulations and implement the best practices. We are your partner in the supply chain, and we can help you understand the current shipping situation.
Keep Everyone in the Loop
We have to believe that there is good news on the horizon, and that freight shipping in the age of COVID will soon return to something resembling normalcy.
Until that time, though, we can still expect certain regulations and requirements to continue impacting our businesses. This will, inevitably, affect your ability to ship your goods at previous levels of consistency.
Take the time to communicate this to everyone in the supply chain. Start with your own staff, but work closely with your shipping partner to schedule new times for pick-ups and deliveries. You should also find ways to let your retailers or consumers know when you’re having difficulties and try to provide them with updated timelines whenever possible.
There’s no doubt that COVID has changed the shipping landscape, but with some time, planning, and new strategies, you can keep moving your products – or reopen your doors – and find new ways to succeed.
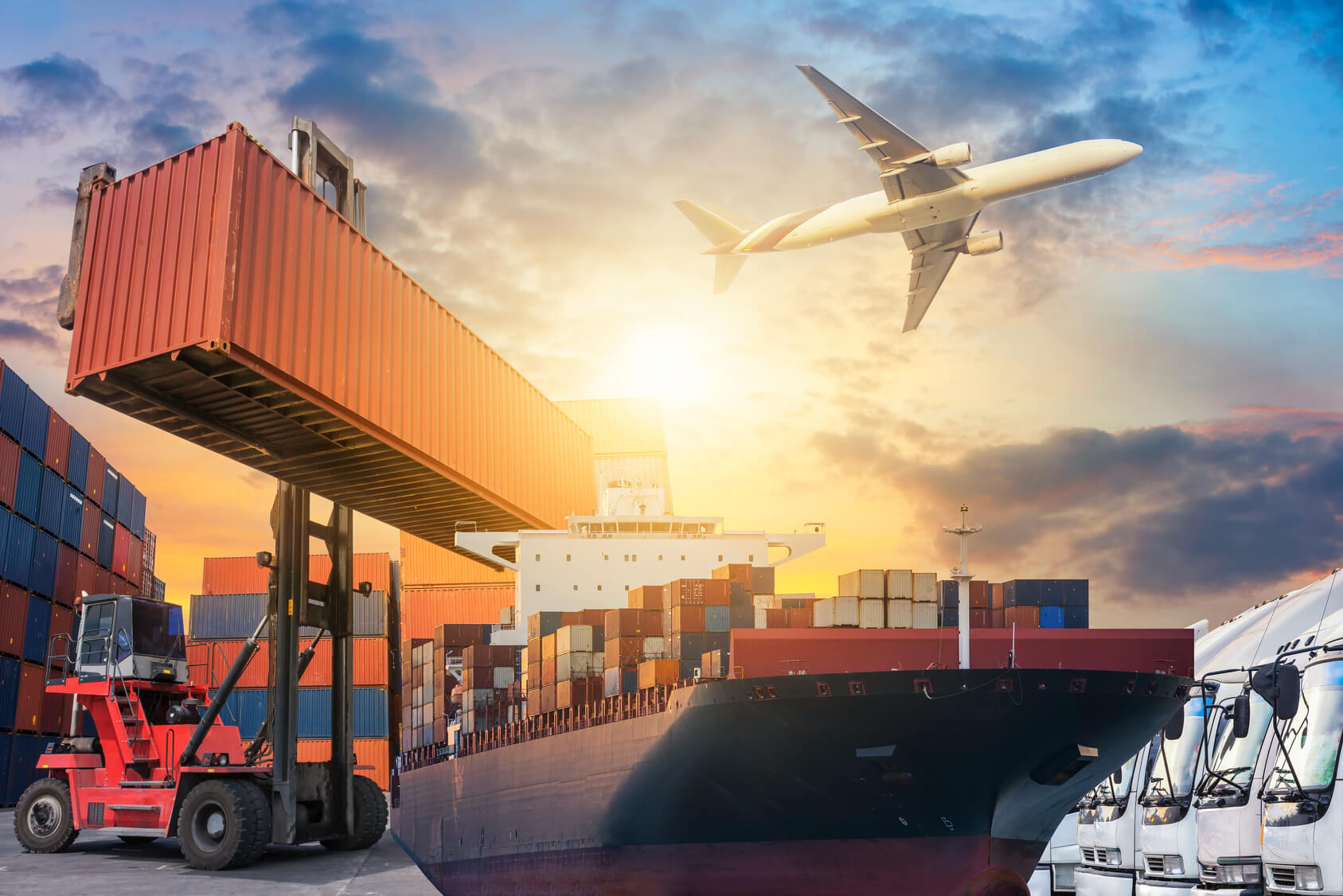
Feb
The practice of trading goods for other goods or services is as old as time itself, however, shipping services have come a long way from utilizing livestock and wagons.
Post-World War II the United States started to shift from mass-production and consumerism to a more service-oriented sector. Both economic deregulation and globalized production create a trade-friendly environment that has the multi-faceted logistics and requirements of shipping services today.
We’ve put together some of the most critical events that have helped shape today’s freight shipping processes. Let’s take a look:
Freight shipping services history
As early as 4000 BC, horses and camels become domesticated and were used to move both people and items. While more efficient than walking, the process was still slow and quantities that could be moved were limited.
Around 3500 BC, the first wheeled vehicle in history was created in the form of a wagon. This increased the quantities able to be moved, however, the human and livestock components kept the process slow. The advent of iron horseshoes sometime around 910 made transportation by horse more efficient. Horse-drawn wagons became a popular mode of shipping, even though it was often slow and dangerous.
The first successful steamboat engine cruised down the Mississippi River in 1787. Steamboats became an alternative for more efficient freight shipping services. Prior to the assistance of a steam engine, rafts and flatboats were used. These methods required manpower and were often slow and arduous with the rafts being left for firewood at their destination, with no way to return them upriver.
A plan to revamp roads and build canals was put in motion in 1807. Canals provide low-cost freight transportation, and improved road systems allow faster connections. These two changes largely triggered westward expansion, with cities and people finding their way west.
In the 1820’s railroad systems peaked and by the end of the century, had a monopoly on the freight industry. This innovative way to move freight was fast, efficient, and required little human intervention. In 1832 Matthias Baldwin built ‘Old Ironside,’ a model locomotive able to go 30 MPH and haul large loads. In 1863, the construction of a railway to connect the Pacific to the Atlantic Ocean began. This ensured safer and faster travel. With this new railway, travel time was cut from six months to six days.
The Transcontinental Railroad was completed in 1869. It brought the Union Pacific Railroad and the Central Pacific Railroad together. It is 3,500 miles long and extends from California through the Sierras and the Missouri River reaching Chicago. Speed and dependability were at an all time high for shipping services, no longer depending on livestock and human capacities.
Transportation companies were regulated in order to stop railroads from charging unfair freight rates and to protect companies from unfair competition in 1887. The Interstate Commerce Act required that railroad rates be “reasonable and just,” but didn’t give the government authority to set specific rates.
At the onset of the 1900s cars became popular in cities, but only the wealthy could afford them. At this time, cities began paving their roads to accommodate this new mode of personal transportation.
In 1935, the Motor Carrier Act passed, regulating the trucking industry. This act set freight-hauling rate regulations restricted the number of hours truckers drove and monitored trucking companies’ range, as well as the type of freight they shipped. Road infrastructures advanced with driver demand.
By the year 1950, about 173 billion ton-miles of commercial inter-city freight was transported by truck. About 15 years later, Eisenhower passed the Interstate Highway System into law, creating a 41,000-mile National System of Interstate and Defense Highways. The intent of the system would safeguard against dangerous roads, inefficient routes, and traffic jams that were barriers to “speedy, safe transcontinental travel.” This would also enable larger trucks to carry more freight on faster schedules.
Freight revenues rose in the 1970s. Trucking moved from carrying less than 1 percent of freight-ton miles to 25 percent, with 75 percent of revenue coming from high-value goods. Large companies were offering truckload service and other companies less than truckload service alongside a system of smaller regional and local carriers. A high-quality highway network made trucking the most reliable service available.
Commercial freight by truck reached 555 billion ton-miles in the 1980s, as it grew along with the interstate system. Federal restrictions loosed on trucking prices and routes. By 1985, commercial truck freight increased to about 650 billion ton-miles.
In the early 1990s, trucking deregulated and the industry saw more independent owners and operators. Deregulation of the intrastate activity of interstate carriers eased the economic mandates initially placed over truckers operating within their borders.
After a US economic recession in 2001, shipping companies witnessed financial gains. A new set of driver hours of service rules went into effect which cut driving time for truckers. The industry was now required to process electronic cargo manifests to Customs and Border Protection for trucks entering the US through all entry ports in Washington, Arizona, and select ports in North Dakota.
As of 2019, trucks moved 11.84 billion tons of freight. The same year, trucking’s revenues accounted for 80.4% of the nation’s freight bill.
Freight shipping services and the future
While shipping services have evolved from horses to boats to freight trucks, the main goal has always been the same; moving goods from one place to another quickly, and safely at the most cost-effective rate.
Today, it is easy to get a shipping quote with the click of a few buttons, and organizing logistics through the supply chain can all be done from anywhere with a computer and internet connection.
This process is likely to continue to evolve as new methods become available. Digital, solar and even electric opportunities may have a future in shipping services.
At Calex ISCS, we are committed to our focus on safety and reliability. We have been “Doing what we say” since 1974. We strive to help you discover the shipping options that can reduce your costs while streamlining your operations, and we are looking forward to what’s next.
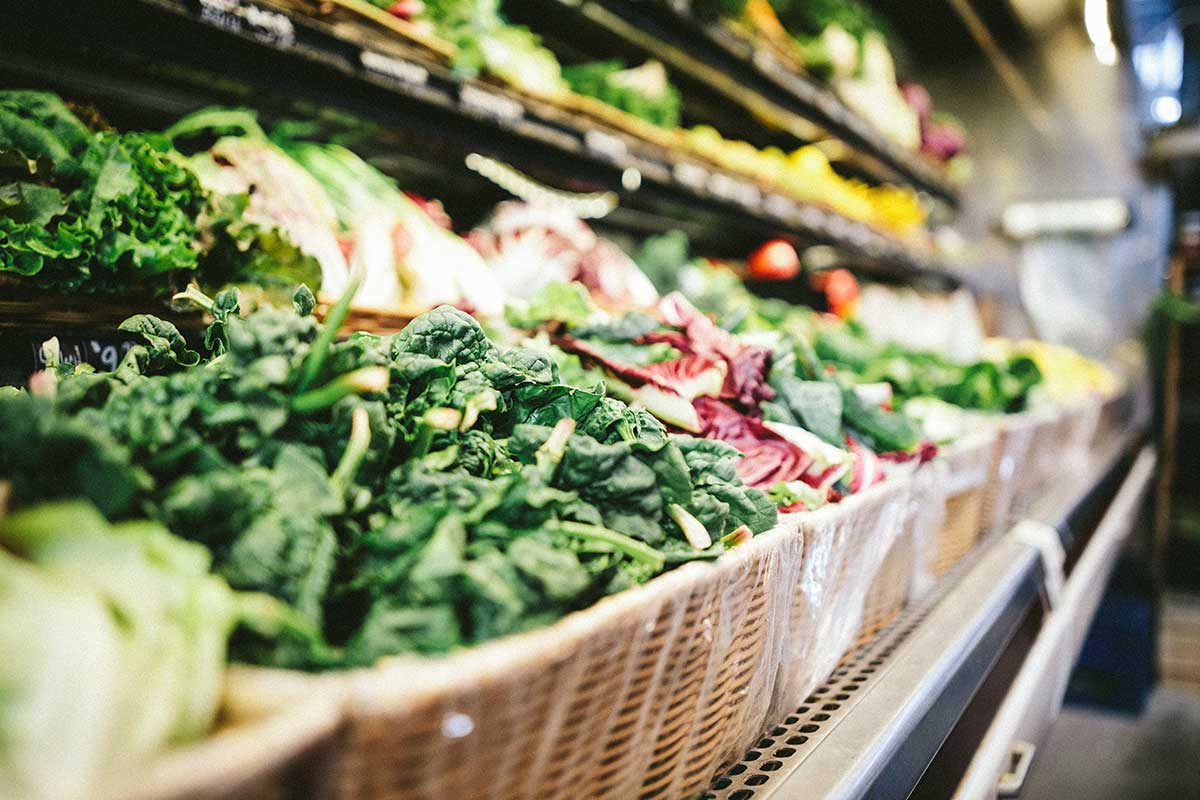
Jan
The produce season is part of the yearly seasonal demand cycle, in which we experience a short-term, predictable surge in shipping volumes throughout different areas of the country.
While we know where the produce season starts, and can prepare for a lot of the increased volume from those places, some surges can crop up in certain places before a shipper can get their drivers and refrigerated trailers to them in an optimal time frame.
As producers attempt to source the transportation and warehousing services they need, shippers are looking to maximize the value of every truckload throughout the season. This can be a pretty profitable arrangement for every party involved, if they are fully prepared for the changes that are common in this season.
Classifying the Produce Season
As the temperatures begin to rise every spring, it’s time to start harvesting the fruits and vegetables and get them out on the road.
Of course, this doesn’t happen all at once. Produce season starts in the southern states and moves northward throughout the summer months.
So, while it’s hard to pin down an exact date, generally speaking, produce seasons starts in southern Florida and Texas in or around March, when the new crops start coming out of the ground.
On top of that, though, produce from Mexico and other Latin American countries begins coming in across the border, causing more shipping spikes in some regions.
These spots of high demand will shift throughout the year, and by the time we reach Q2, most of the produce is coming from northern Florida and Texas, but now California, Georgia, and the Carolinas are starting the chip in.
How the Produce Season Impacts Transportation and Warehousing Services
The seasonal shipping spikes that come with produce season can cause some difficulties throughout the country, as some rates may go up and down along with demand.
Shippers must be able to prioritize the must-move freight and ensure that it arrives at its destination on time. They will need to be flexible enough to handle sudden spikes in demand or sudden shifts in pickup and drop-off locations throughout the season.
Shippers will also start looking for ways to maximize their routes and optimize their turnaround times by working with producers who are delivering to nearby outlets.
This is, of course, just a few of the considerations.
There are a couple other big ones that require a little more in-depth discussion.
Refrigerated Shipping is Hugely Important
During the produce season, the ability to ship perishable goods while maintaining their integrity is critical to the supply chain. In other words, refrigerated shipping is the top priority for producers who need to move goods any significant distance.
Uncontrolled shipping temperatures for produce could lead to huge losses for the producer and the shipper. There are also a number of public health issues that need to be considered, and any breaches could lead to a number of penalties in the future – and, of course, a lot of damage to the company’s reputation.
That being said, refrigerated shipping offers a lot of great benefits. There are so many more products available these days, and these modern transportation solutions have made it possible to move them all across the country.
Now, it’s possible for producers to meet the growing demand for a huge variety of perishable goods, so different types of produce are reaching more areas than ever before.
Driver’s Must Be Strategically Scheduled
Professional drivers are a limited resource, and they’re still in very short supply.
This is an issue that every transportation company is dealing with these days, and it requires a lot of pre-planning to keep the trucks out on the road and keep your products moving.
This problem is certainly exacerbated in the produce season, when we have to be even more flexible and react more quickly in order to make sure every spike in demand has a truck and an experienced driver ready to respond.
How Did 2020 Impact Produce Shipping?
The COVID pandemic has had an impact on every industry, and that includes growers and transporters right along with everyone else.
Coming into the produce season this year, though, means that the industry has a better understanding of the “new normal” and can ramp operations back up to something that resembles pre-Corona times.
Everything from how our drivers interact with shippers and receivers to how we provide warehouse services has changed, but it’s all part of dealing with an ever-evolving industry.
Are You Ready for Produce Season?
The yearly spike in demand for fresh produce is a predictable occurrence, but it always demands a high level of flexibility and determination to provide safe and effective transportation.
There is always a chance to encounter something that could disrupt the normal movement of your products, so be sure to begin your planning well in advance of the season. Start forecasting your needs now, and contact us to explore your options.
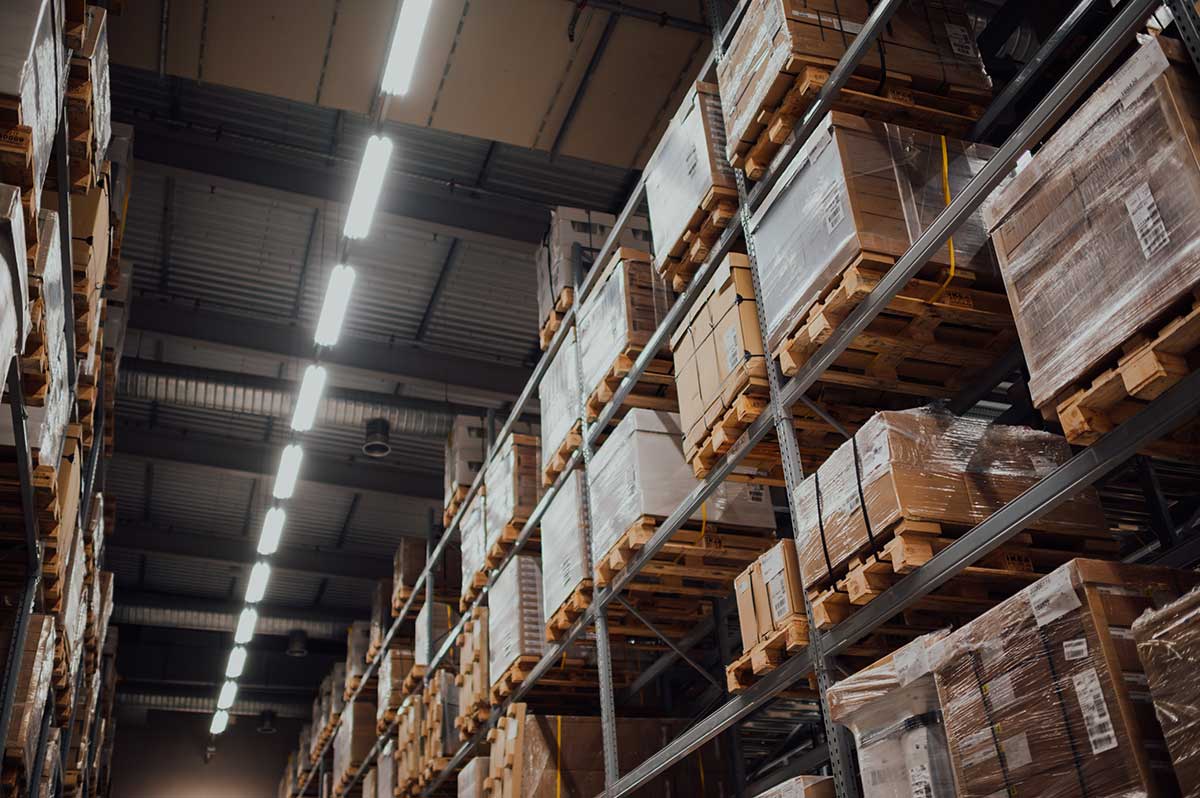
Jan
The warehousing and transportation industry is filled with a wide variety of acronyms, specialized terminology, and no small amount of general jargon.
If you’ve been working with a professional shipping company for any length of time, you’ve probably become familiar with several of them already.
Even so, there are always one or two acronyms that you may not be familiar with, or some terms that one company may use that others do not. Rather than just nodding your head and assuming the meaning from the context, let’s take a moment to go over some of the more important terms that will help you navigate the world of warehouse storage and transportation services.
BOL – Bill of Landing – This is mandatory paperwork that tells the driver and the trucking company everything they need to know to process and complete the shipment. It is essentially a receipt that is legally binding. It should include everything from the shipping address to the packaging type to a simple description of the products.
DC – Distribution Center – The facility in which a manufacturer can store inventory while it is waiting for transportation to the intended final outlets.
EDI – Electronic Data Interchange – There are several documents in the transportation and warehousing industries that must be reliably moved around and saved. Invoices, BOLs, and other documentation fall into this category.
ELD – Electronic Logging Device – This device is required by the FMCSA for all trucks out on the road. It is intended to record the driver’s actual time behind the wheel and ensure that they are complying with the hours-of-service regulations.
FAK – Freight of All Kinds – This is a classification that covers several different types of products in a single load. This is a very common situation because it can simplify the rating and pricing (though it is possible for this to lead to higher rates than those with specific classifications).
FMCSA – Federal Motor Carrier Safety Administration – The federal agency that establishes rules and regulations regarding the transportation industry.
FOB – Free on Board – This designation is used when the seller transfers the liability and ownership of a product to the buyer. It can also be used to determine which party at a physical location is responsible for the payment of freight charges.
GVW – Gross Vehicle Weight – This refers to the total weight of the vehicle and its cargo together. This will have an impact on the GVWR, which can limit the amount of product carried by any given vehicle.
GVWR – Gross Vehicle Weight Rating – This is the maximum allowable operating weight of a vehicle (which will usually be specified by the manufacturer). The rating includes the vehicle’s chassis, body, engine, engine fluids, fuel, the driver (and any passengers), and, of course, the cargo.
JIT – Just-in-Time – There isn’t a lot of room for error in a transportation schedule, and this informs the company that the products they are carrying must arrive at their destination at the specified time.
LTL/LCL – Less-Than- Truckload/Containerload – This refers to a trailer or container that is loaded with products from more than a single shipper. This occurs when one manufacturer is not producing enough to fill the entire trailer in a single shipment.
NMFC – National Motor Freight Classification – This is how you categorize your freight, and it is defined and regulated by the National Motor Freight Traffic Association. Shippers need to know the NMFC codes because they have a direct impact on the shipping charges. Currently, there are 18 freight classes (from class 50 to class 500).
RTV – Return to Vendor – If a customer rejects the shipment after a buyer’s inspection, it falls into this category. It says that the freight is waiting to be shipped back to the supplier where it can be replaced or repaired.
3PL – Third-Party Logistics Provider – Refers to a logistics company (rather than an in-house department) that provides a range of services, including transportation, warehousing, pick and pack, and other solutions that contribute to the accurate and effective movement of freight from point A to point B.
TL – Truckload – This specifies the amount of freight that is required to fill a truck (or at least to qualify for the truckload rate). Anything less will fall into the LTL category.
Talking the Talk
We understand that if you haven’t dealt with transportation services in the past, a lot of the vocabulary and acronyms may be pretty new to you. On the other hand, if you’ve been working with warehouses and shippers for some time, a lot of the terms included here may seem a little self-evident.
Either way, it’s worth taking the time to familiarize (or re-familiarize) yourself with these common industry terms so you can easily get in on the lingo and start talking the talk.
And, of course, this is just the beginning. If you’d like to see more, be sure to check out the U.S Department of Transportation’s Freight Glossary and Acronyms page.
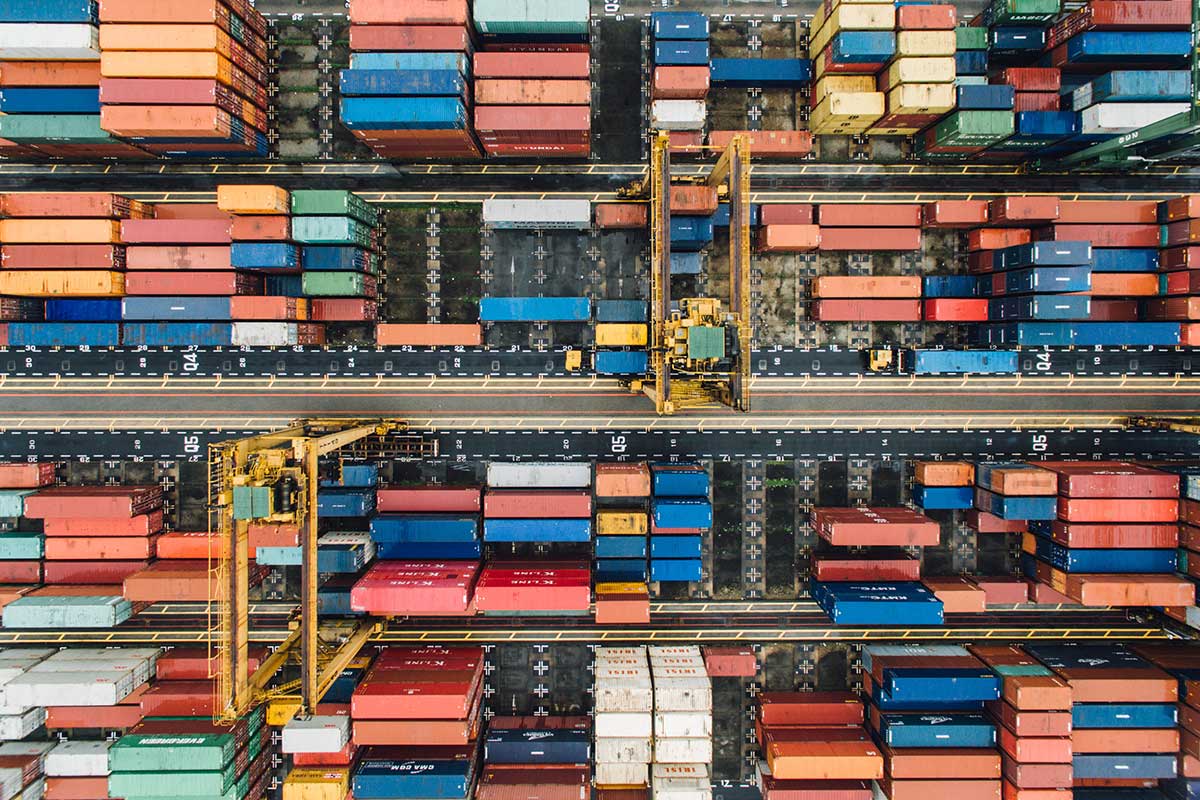
Jan
Often, producers and shippers work under the assumption that the prices they pay to transport their freight are fixed costs that won’t change (at least not without a significant struggle).
However, there are some simple and important things you could start doing today to reduce your supply chain shipping costs and start to improve a number of your efficiencies along the way.
Controlling your shipping costs should be one of your highest priorities as a producer, but it is also important to understand that there are simply some logistical issues that will remain out of your control. Fuel prices, delays at ports and warehouses, and any laws and regulations (such as the ELD mandate in the U.S.) surrounding certain types of goods will all contribute to the final costs.
So, while some parts of modern logistics will remain out of your control as a shipper or producer, there are still some important elements of this process that will help keep your prices down. As you work to streamline your supply chain, consider some of the following:
1. Increase Delivery Lead Times
Effective logistics requires a lot of forward planning. When you can provide significant advanced notice to your carrier about your future loads – i.e., increase your lead times – your carrier can also optimize their trucks, truck space, and drivers.
Anytime one of our trucks has to sit idle at any facility, it can really increase costs. If you can provide the right information, though, it’s easier to streamline your transportation services and potentially pass some of those savings on to the client.
2. Increase Your Packaging Options
There was a time when any old packaging solution would do, since you were only charged based on the product’s weight. Now, there is a dimensional rating to your packages, too, which means that inefficient packaging can add a lot to your final costs.
The size of the box now plays a huge part in a cost-effective shipment. If you’re shipping a box that could carry several more pounds of product than was actually in it, you are wasting money. At the same time, if you’re filling that excess space with packing materials, you’re further increasing your costs.
Make sure you have a variety of box sizes available so you can choose the right size for the right shipments. You may have to increase your storage space for the various boxes, and train your packing staff to choose the right one for a given shipment, but the money you save in return will be worth it.
3. Reduce the Number of Required Pallet Spaces
It’s important to optimize the cube of a product. If you can stack your boxes so they take up fewer pallet spots, it can save you a lot on your next shipment. You will be able to get more of your product onto a pallet and into a trailer, which means you’ll take up less space and be charged less in the long run.
Building a more efficient pallet can help you consolidate shipments (so fewer shipments are required), which means transportation managers can plan their shipments far more effectively.
4. Location Matters
You can improve your supply chain management by working with a transportation company that is based close to your ship-to points. This makes it easier to fit your shipment into an otherwise busy schedule or a crowded trailer.
The same thing applies to your warehousing solutions. If you are regularly shipping to specific locations, it may improve your ability to move product by using a warehouse that is closer to your customers. This, in turn, will contribute to a reduction in your transportation costs.
5. Use Fewer Carriers
While there can be some benefits to maintaining a large number of partners in some areas of your business, there comes a time when you need to streamline your contracts to reduce your costs. You may have gone through a lot of effort to find the carriers who provide the best prices, or you may have tried to find the best price for each individual route, but this isn’t always the most optimal way to deal with different transportation companies.
As you reduce the number of companies you work with, the amount of business you can provide for a single carrier will go up. Then, you can start looking at potential discounts for larger volumes. You may find that each individual route may not have the very best rate possible, but your overall savings could shoot up.
6. Think about Logistics During the Design Phase
It’s important to think about how a product will be packaged and shipped while you are still in the design phase. Elements of packaging can help optimize your pallets and cut down on unnecessary shipping costs.
Warehousing and transportation costs make up a large part of your supply chain costs, while packaging costs are likely very small in comparison. In other words, it will be worth your time to invest in smart packaging design upfront so you can reap the transportation benefits later.
7. Automate Your Logistics
Automated and managed logistics can help you track your shipments from point A to point B so you can continually watch for problem areas that can be improved over time. These may seem like small changes at first, but as you continue to gather data and make immediate changes, the benefits will build up.
This kind of visibility into your supply chain will also help you avoid unexpected problems and costs. You’ll be able to keep an eye on your routes and make quick decisions to avoid disruptions in your shipments.
Simple Changes for Big Returns
A lot of these suggestions may seem like common sense, but you may be surprised how often shippers and producers fail to incorporate them into their supply chain activities.
This could be because they are too accustomed to the way things have always been or simply don’t have the time or personnel to look into alternatives.
Since transportation costs make up such a large part of the overall supply chain spend, though, it will be worth the time and effort to streamline your logistics activities and reduce your overall costs.
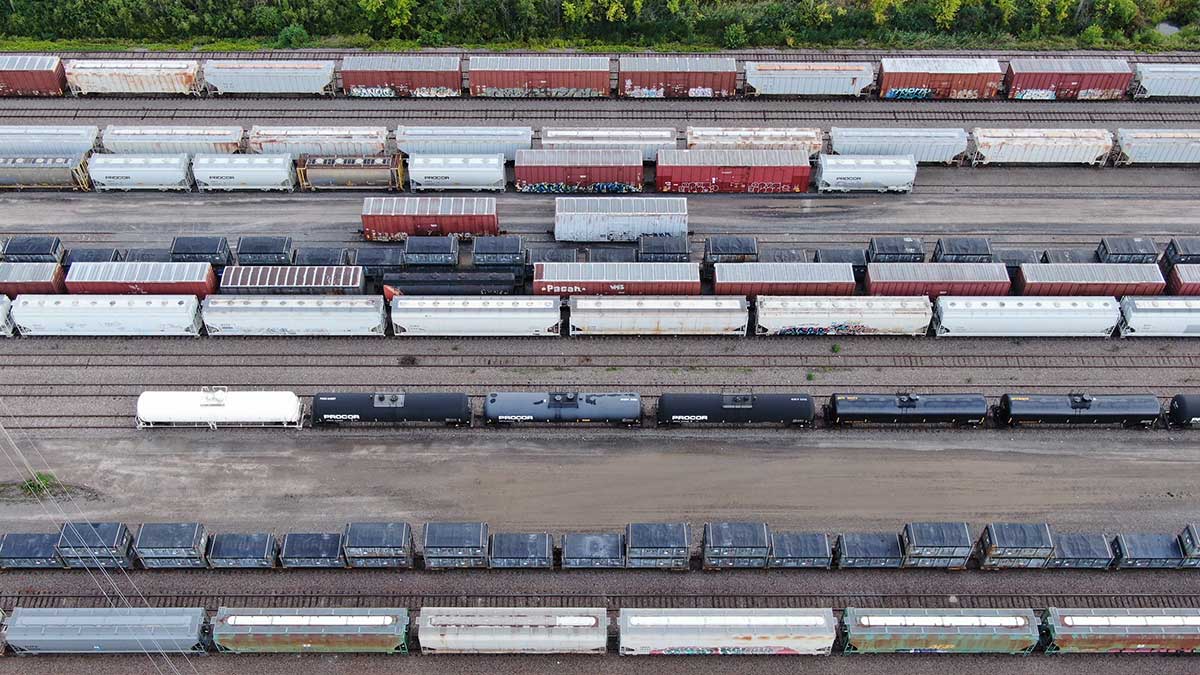
Jan
Top 3 Red Flags of Freight Shipping Companies and How to Avoid Them
SEO .COM0 comments Uncategorized
Freight shipping companies can have a huge impact on your supply chain, which means you need to ensure that whoever you partner with is capable of saying what they can do and always doing what they say.
Any breakdown in this process can lead to a decline in profits and reputation.
Previously, we discussed some important factors to consider when choosing a shipping company.
Now, it’s time to take a look at some of the common red flags that should tell you when a company may not be the one you want to go with. We’ll also suggest some simple things you can do to avoid these potential issues.
1. Rates that Are Clearly Too Low
If something is “too good to be true,” assume that you have discovered an inescapable fact about the quote you just received.
There are some fraudulent companies out there that will say they will accept a load for a significantly reduced rate just to get you to sign on. Their prices will be extremely tempting – especially compared to what all the well-established companies charge – and they’ll have some kind of explanation or gimmick for why they can make this offer.
However, the simple fact is that the costs of fuel and the increased rates for professional drivers continue to go up, leading to increased prices on every front. This has impacted everyone in the supply chain.
If you happened to stumble across the one company in the entire country that doesn’t seem to be affected by these increases, then chances are you really haven’t.
All you’ve done is stumbled across someone who is attempting to run a scam.
How to avoid this issue:
Don’t just accept the first quote you’re given. Take the time to field a few quotes because, at the very least, this should give you a good baseline from which you can judge every offer.
Don’t just assume that some wonderfully low price is close to the industry standard and you’re just getting a great “sign on” deal.
If you see that a quote is excessively lower than the baseline, you may have reason to question their sincerity or their ability to complete the delivery.
2. Fuel Advance Fraud
This is, unfortunately, something that is all too common in the industry. It’s a type of fraud that involves one party claiming to be a carrier and “selling their shipping services” to unsuspecting producers. This party will then turn around and try to sell the work to an actual carrier for a higher price – higher than the producer agreed to pay.
In order to accomplish this, the fraudulent party must obtain documents from actual carriers and then alter them to make it look like they are representing a legitimate company.
Once the load is picked up, the scammer will fax the necessary information from the actual company to producer and requests a fuel advance on the load – which they will then take and run away, leaving everyone else with the actual financial burden and goods that aren’t going anywhere.
How to avoid this issue:
Always check the credentials of the shipping company you work with. Make sure that the DOT/MC number match the numbers that your carrier has submitted. Take the time to verify any contact information you are given, because the existence of a website is not enough to prove that a real company exists behind your shipping services quote.
Fuel advance scams also try to take advantage of your need for speed. They’ll pray on your anxiety over on-time shipments and claim that the driver has no money and won’t be able to complete the delivery without a fuel advance. So, take your time, verify your data, and don’t listen to these claims.
3. Too Many or Too Few Reviews
While a professional freight shipping company isn’t going to have online reviews in the same way that businesses in the hospitality, medical, or consumer industries do, you should be able to drum up some legitimate reviews for any shipping services.
You can check their website for customer testimonials or explore their social media presence or even see if Google has a rating for the company.
If you can’t find any reviews at all, this could indicate that they simply don’t have the experience or the successes for customers to talk about.
On the other hand, if you find nothing but a stream of 5-star reviews that are posted by someone with a loose grip on the English language and seems to repeat the same sentence over and, then there may be some issues going on.
How to avoid this issue:
Take the time to seek out reviews for the company you are going to work with. Better yet, ask the carrier if they can give you a list of companies they’ve worked with in the past and if they can show you some case studies involving previous clients.
Your shipment is too valuable to take any risks with your intermodal transportation services. Keep an eye out for red flags just like these and make sure that your cargo gets safely and efficiently from your location to its final destination.
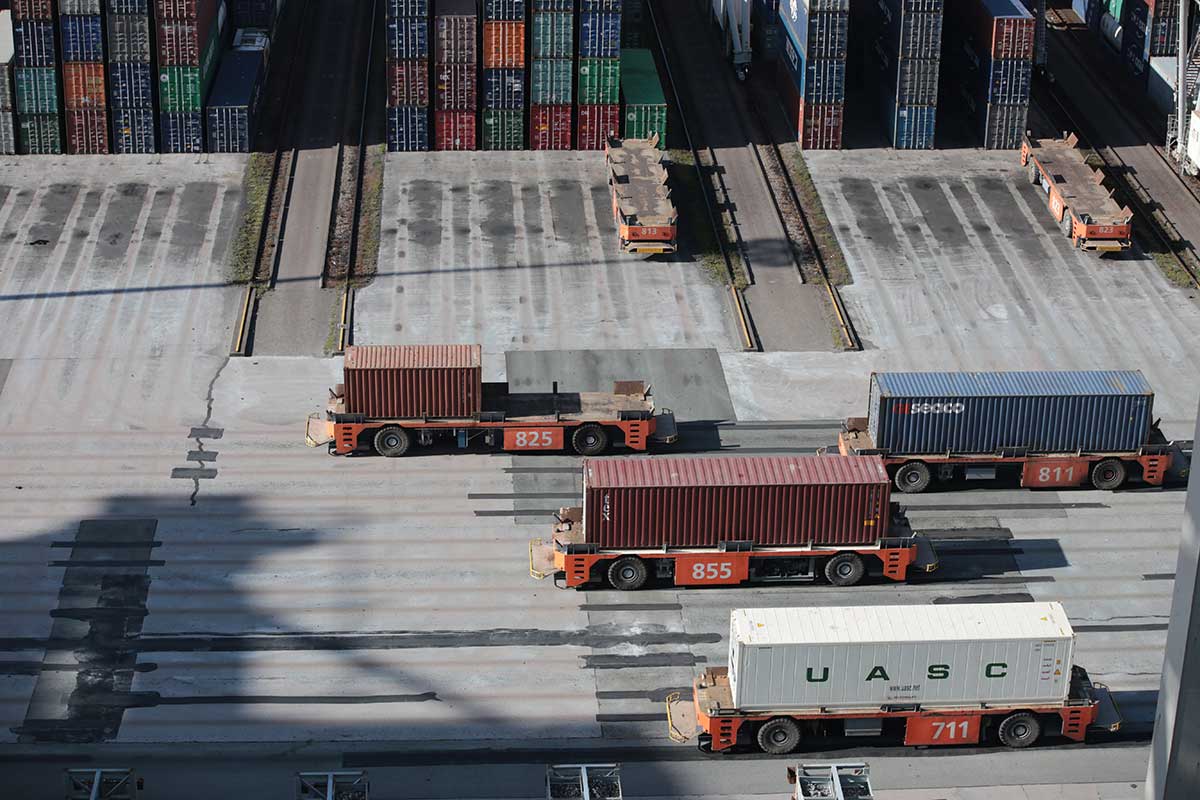
Jan
The safe and efficient transportation of your goods is a critical part of the supply chain, so when you choose a shipping company, you need to consider a wide range of criteria.
It’s not just about choosing the one with the cheapest prices (although cost is obviously a factor). It’s about weighing the pros and cons of every offer or quote you receive and comparing their services to your exact needs. It’s about finding a reliable partner that can support your efforts to get your product to market.
So, if it’s about more than just the cost, what should you look for in a shipping company?
1. An Infrastructure That Can Support Your Supply Chain
Many companies require more than occasional transportation services. Their business model requires a constant flow of regular shipments, intermodal transportation, and safe, reliable warehousing.
If you fall into this category, you need to make sure that your shipping company has the resources to provide that level of work. Do they have the drivers? The trucks? The refrigerated shipping options? Will they be able to keep your products moving to meet demand?
2. Extensive Experience
A freight service that has been in business for some time has likely already seen all kinds of issues on the road, in distribution, behind the scenes, and everywhere else problems can possibly appear.
And, if they’re still in business, that means they figured out how to deal with each of those problems and came out on top.
You need drivers and warehouse managers and other staff members who can make the entire process of loading, shipping, and unloading go as smoothly as possible.
3. A Priority on Safety
At Calex, safety is priority ONE. Whether that means the safety of your products or the safety of our people, we have instituted several policies that protect our people and your inventory.
Fleet managers need to ensure the safety of every shipment by making sure all the trucks are maintained to the highest standards (or replaced with newer models) and that your inventory is always packed and shipped correctly. Drivers should be highly trained and instructed to obey all traffic laws.
4. A Commitment to Professionalism
Everyone who is involved in your freight shipping service should be completely professional in their dealings. Whether they’re interacting with the people at your establishment or at the final delivery location, they need to look and act like professionals who understand the importance of your business.
The driver may just be delivering your goods, but you’re the one that chose your shipping service, so how they act will reflect on your brand. Make sure you work with a company that understands that connection.
5. Highly Trained Support Personnel
Effective shipping is a team effort, and the dispatchers, mechanics, managers, and many more people contribute to the efficiency of your shipment. Your products need to be processed and tracked, and drivers need to be in communication with people who provide the information they need.
Dock workers need to make the loading and unloading process seamless, dispatchers need to assign routes effectively, and mechanics need to keep everything in the best shape possible.
Our drivers depend on the staff behind the scenes to ensure they can deliver your products safely and on time.
6. Regulatory Compliance
Every state has different regulations on how certain products are handled or on the emission levels of large trucks. If your shipping service isn’t in line with all these requirements, it could lead to fines or other problems.
Older trucks may not meet the current regulations in some states, so make sure the company’s fleet is filled with newer vehicles. It’s also important to make sure every truck receives the necessary maintenance before it hits the road.
7. The Flexibility to Change with You
You likely won’t need the same level of transportation services throughout the year. Seasonal shifts or market trends can change your needs overnight.
If you are locked into a specific contract, it could end up costing you more money than necessary. Make sure that the services you use are able to adapt to your needs and scale up or down as your business goes through its natural changes.
Why You Need More Than Low Prices
While you should absolutely look for the most cost-effective freight services, it’s important to remember that if the price seems “too good to be true,” there’s a good chance that some corners are being cut somewhere.
If those corners include the safety measures, or proper driver training, or even vehicle maintenance, then, well, your results may reflect the price.
When you choose a shipping company, it’s important to find the optimal balance between price and reliable services. Keep all of the elements we’ve listed here in mind, and choose wisely.