Blog
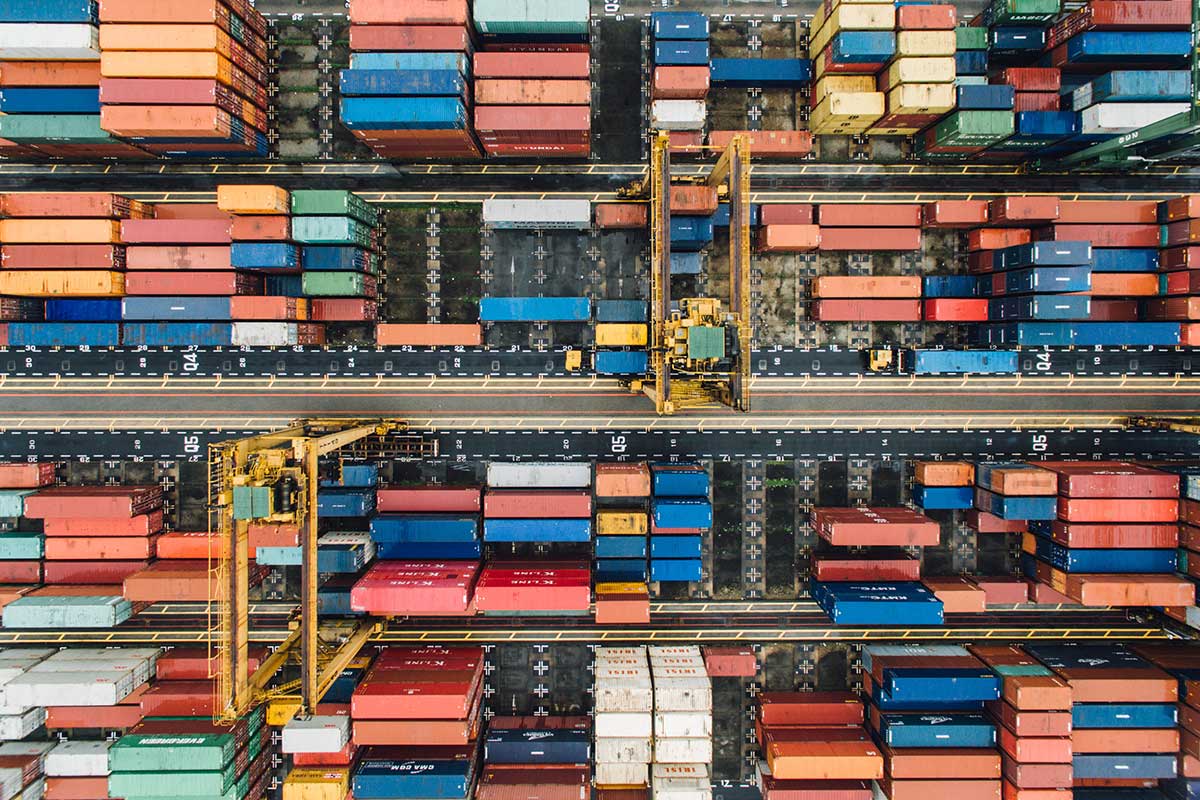
Jan
Often, producers and shippers work under the assumption that the prices they pay to transport their freight are fixed costs that won’t change (at least not without a significant struggle).
However, there are some simple and important things you could start doing today to reduce your supply chain shipping costs and start to improve a number of your efficiencies along the way.
Controlling your shipping costs should be one of your highest priorities as a producer, but it is also important to understand that there are simply some logistical issues that will remain out of your control. Fuel prices, delays at ports and warehouses, and any laws and regulations (such as the ELD mandate in the U.S.) surrounding certain types of goods will all contribute to the final costs.
So, while some parts of modern logistics will remain out of your control as a shipper or producer, there are still some important elements of this process that will help keep your prices down. As you work to streamline your supply chain, consider some of the following:
1. Increase Delivery Lead Times
Effective logistics requires a lot of forward planning. When you can provide significant advanced notice to your carrier about your future loads – i.e., increase your lead times – your carrier can also optimize their trucks, truck space, and drivers.
Anytime one of our trucks has to sit idle at any facility, it can really increase costs. If you can provide the right information, though, it’s easier to streamline your transportation services and potentially pass some of those savings on to the client.
2. Increase Your Packaging Options
There was a time when any old packaging solution would do, since you were only charged based on the product’s weight. Now, there is a dimensional rating to your packages, too, which means that inefficient packaging can add a lot to your final costs.
The size of the box now plays a huge part in a cost-effective shipment. If you’re shipping a box that could carry several more pounds of product than was actually in it, you are wasting money. At the same time, if you’re filling that excess space with packing materials, you’re further increasing your costs.
Make sure you have a variety of box sizes available so you can choose the right size for the right shipments. You may have to increase your storage space for the various boxes, and train your packing staff to choose the right one for a given shipment, but the money you save in return will be worth it.
3. Reduce the Number of Required Pallet Spaces
It’s important to optimize the cube of a product. If you can stack your boxes so they take up fewer pallet spots, it can save you a lot on your next shipment. You will be able to get more of your product onto a pallet and into a trailer, which means you’ll take up less space and be charged less in the long run.
Building a more efficient pallet can help you consolidate shipments (so fewer shipments are required), which means transportation managers can plan their shipments far more effectively.
4. Location Matters
You can improve your supply chain management by working with a transportation company that is based close to your ship-to points. This makes it easier to fit your shipment into an otherwise busy schedule or a crowded trailer.
The same thing applies to your warehousing solutions. If you are regularly shipping to specific locations, it may improve your ability to move product by using a warehouse that is closer to your customers. This, in turn, will contribute to a reduction in your transportation costs.
5. Use Fewer Carriers
While there can be some benefits to maintaining a large number of partners in some areas of your business, there comes a time when you need to streamline your contracts to reduce your costs. You may have gone through a lot of effort to find the carriers who provide the best prices, or you may have tried to find the best price for each individual route, but this isn’t always the most optimal way to deal with different transportation companies.
As you reduce the number of companies you work with, the amount of business you can provide for a single carrier will go up. Then, you can start looking at potential discounts for larger volumes. You may find that each individual route may not have the very best rate possible, but your overall savings could shoot up.
6. Think about Logistics During the Design Phase
It’s important to think about how a product will be packaged and shipped while you are still in the design phase. Elements of packaging can help optimize your pallets and cut down on unnecessary shipping costs.
Warehousing and transportation costs make up a large part of your supply chain costs, while packaging costs are likely very small in comparison. In other words, it will be worth your time to invest in smart packaging design upfront so you can reap the transportation benefits later.
7. Automate Your Logistics
Automated and managed logistics can help you track your shipments from point A to point B so you can continually watch for problem areas that can be improved over time. These may seem like small changes at first, but as you continue to gather data and make immediate changes, the benefits will build up.
This kind of visibility into your supply chain will also help you avoid unexpected problems and costs. You’ll be able to keep an eye on your routes and make quick decisions to avoid disruptions in your shipments.
Simple Changes for Big Returns
A lot of these suggestions may seem like common sense, but you may be surprised how often shippers and producers fail to incorporate them into their supply chain activities.
This could be because they are too accustomed to the way things have always been or simply don’t have the time or personnel to look into alternatives.
Since transportation costs make up such a large part of the overall supply chain spend, though, it will be worth the time and effort to streamline your logistics activities and reduce your overall costs.